Anodizing Finishing Services from China
Vertex’s finishing service to anodize your unique parts.
Vertex offers the following anodizing colors:
- Gloss, Matte, Texture, Patterns.
- Silver, Red, Purple, Pink, Green, Blue, Brown, Orange, Gold, etc
Save 30% on average!
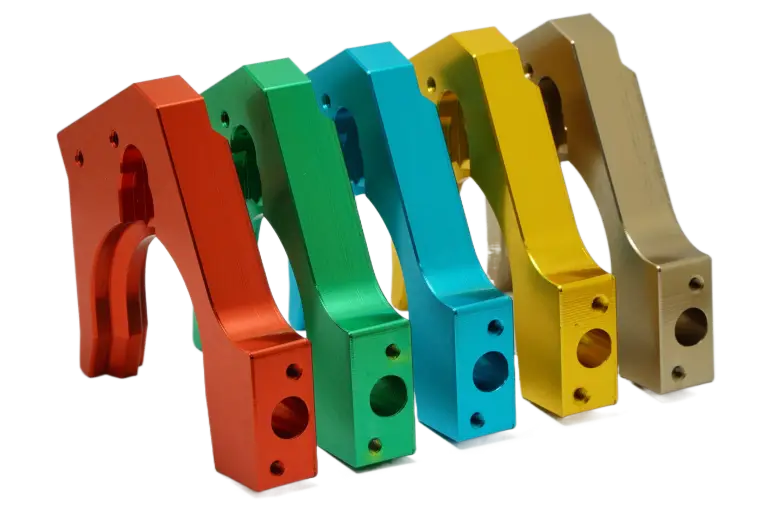
Anodizing Overview And Advantages
Anodizing electrolytically creates a durable oxide layer on aluminum for superior protection and aesthetics.
By passing an electric current through an electrolytic bath, a tough oxide layer forms that resists wear and corrosion while accepting color dyes for vibrant, long-lasting finishes.
The resulting anodized surface offers enhanced durability, insulation, and visual appeal. This makes anodizing a popular technique to extend product life, improve performance, and achieve a polished look across industries.
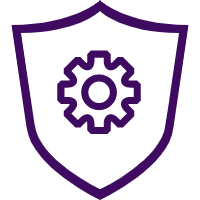
Anodizing creates a thick oxide layer on the aluminum surface. This layer, being much harder than the aluminum itself, offers enhanced protection against chipping, peeling, and scratching, ensuring the component's longevity.
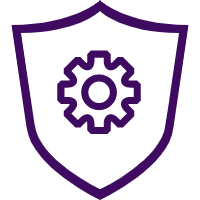
Anodizing creates a thick oxide layer on the aluminum surface. This layer, being much harder than the aluminum itself, offers enhanced protection against chipping, peeling, and scratching, ensuring the component's longevity.
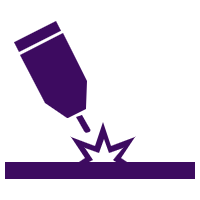
The protective oxide layer formed during the anodizing process acts as a barrier against environmental factors such as moisture, salts, or other corrosive agents. This protection ensures that aluminum parts remain unaffected by rust or corrosion, especially in challenging conditions.
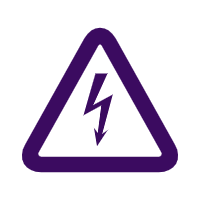
The oxide layer that results from anodizing acts as an insulator. This insulation property can be crucial in electronic applications where specific components must be electrically non-conductive to function correctly.
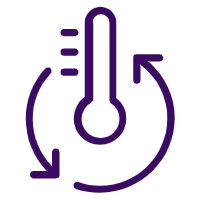
Certain types of anodizing can enhance the aluminum's thermal insulation properties, making it ideal for applications where heat retention or dissipation is a factor.
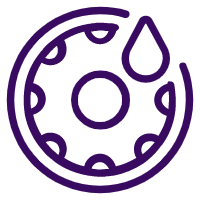
Certain types of anodizing, like Teflon-impregnated hardcoat anodizing, can improve the lubrication properties of aluminum parts, reducing friction in moving components.
Types Of Anodizing Offered By Vertex
Anodizing Type II, commonly known as “Matte,” employs a sulfuric acid anodizing procedure. This results in a consistent oxide layer on aluminum, enhancing corrosion resistance and yielding a non-reflective, matte appearance. This method supports a range of color dyeing choices, offering both protective and aesthetic benefits. The film thickness for Anodizing Type II is 8-12 μm (clear) or 12-16 μm (black/color).
Color: Clear, black, blue, red, gold or customization supported. (Any RAL code or Pantone number)
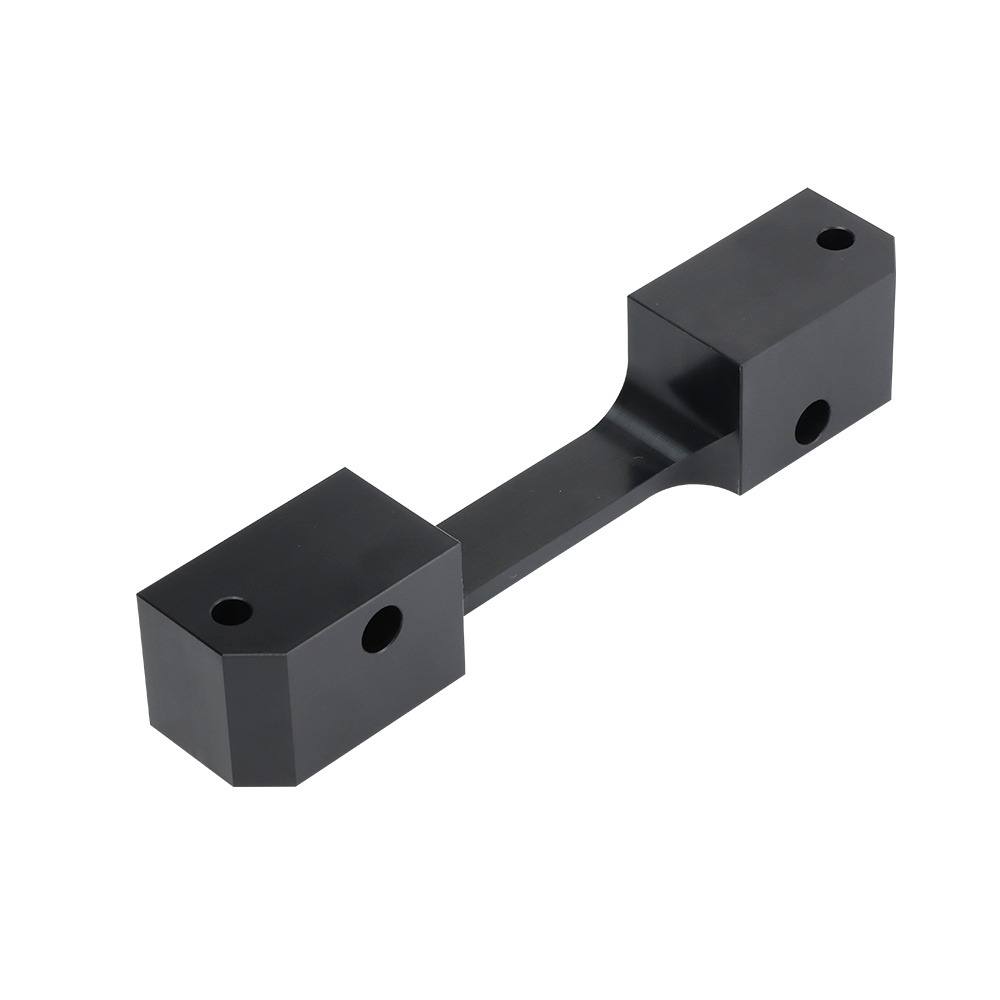
Anodizing Type II (Glossy) represents a modification of the conventional sulfuric acid anodizing process. It introduces a more substantial oxide layer on aluminum, guaranteeing robust protection. This distinctive method yields a lustrous, glossy finish, enhancing the part’s visual allure while preserving its heightened durability. The film thickness for Anodizing Type II is 8-12 μm (clear) or 12-16 μm (black/color).
Color: Clear, black, blue, red, gold or customization supported. (Any RAL code or Pantone number)
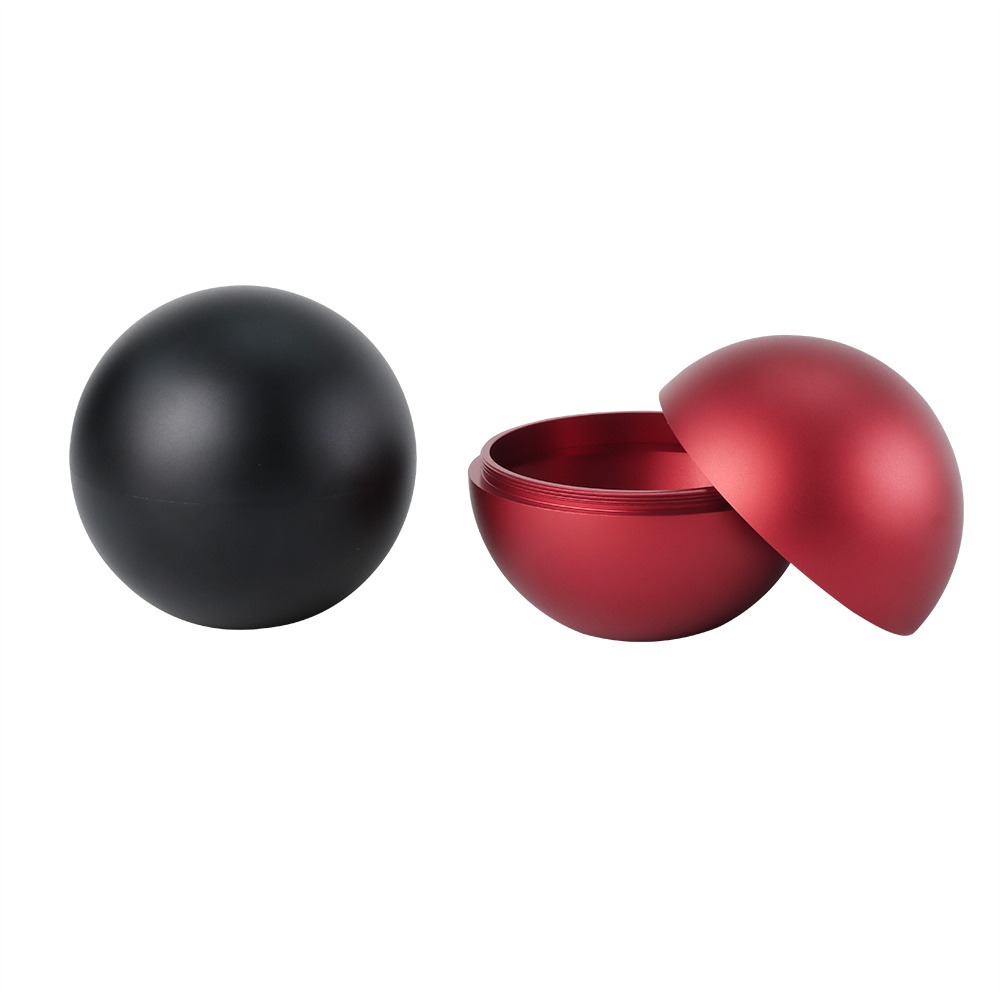
Anodized Type III, commonly referred to as “Hardcoat,” employs sulfuric acid to generate a densely packed oxide layer on aluminum. This procedure yields heightened wear resistance and electrical insulation. The substantial, durable finish, often exhibiting a darker hue, proves resilient in challenging environments and under rigorous use. The film thickness for Anodizing Type III is 25-50 μm.
Color: Nature, black or other colors
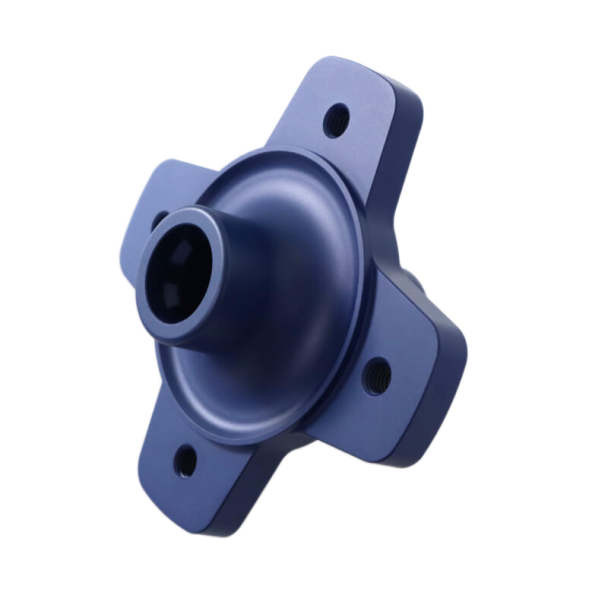
Cleaning: Parts are cleaned in a non-etching, alkaline solution to remove surface impurities, ensuring a flawless anodizing result.
Rinsing: Cleaned parts are thoroughly rinsed with deionized water to remove any remaining cleaning agent residues.
Etching: Immersed in an acid bath (usually caustic soda), parts undergo etching to achieve a matte appearance or to prepare for further processing.
Desmutting: This neutralizes and removes surface contaminants, ensuring a pure aluminum surface for the subsequent anodizing process.
Anodizing: Parts are submerged in an electrolytic solution, typically sulfuric acid, and electrical current is passed to form the protective oxide layer.
Coloring (optional): After anodizing, parts can be dyed by immersing them in a bath containing organic or inorganic colorants.
Sealing: The anodized surface is sealed, typically in a hot water bath, to close pores, enhancing corrosion resistance and color retention.
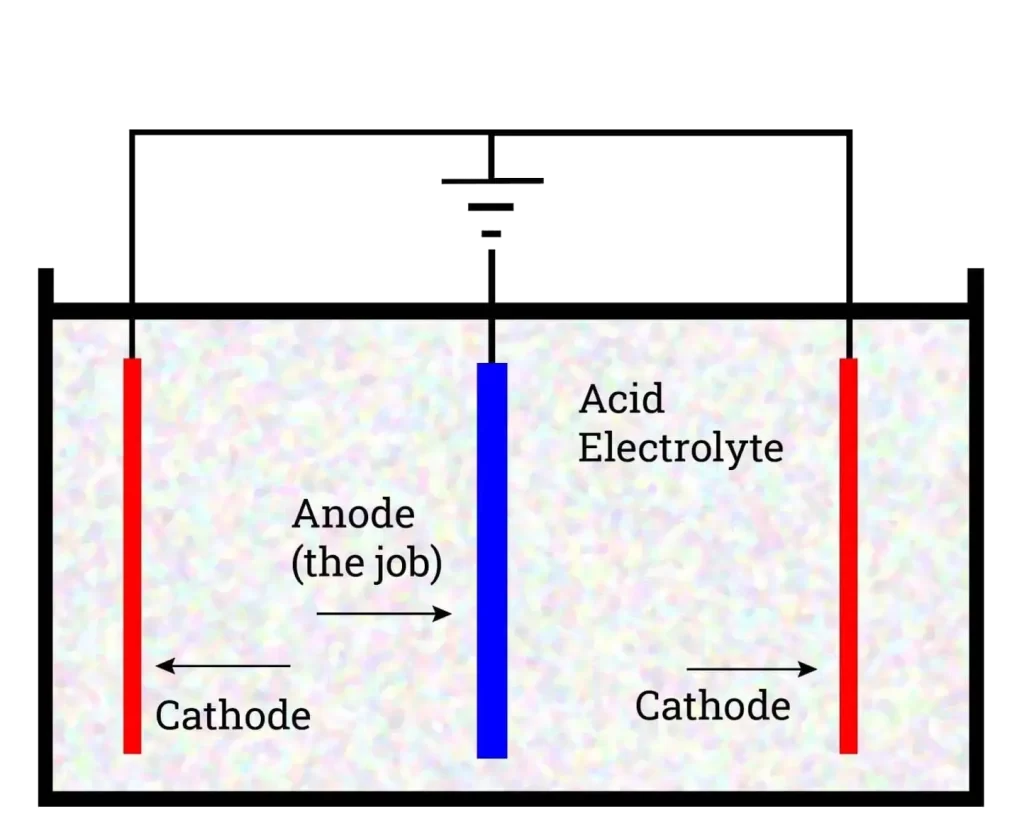
What Metal Cannot Be Anodized?
While many metals can be anodized, common ones include aluminum and its alloys. Metals such as iron and steel generally cannot be anodized because the process relies on forming a stable oxide layer, which these metals do not readily develop.
What Everyday Items Are Anodized?
Anodized aluminum finds widespread use in everyday items such as cookware, automotive parts like rims and trim, electronic devices including smartphones and laptops, sporting goods like bicycle frames and golf clubs, architectural elements such as window frames and handrails, and aerospace components.
How Can You Tell If The Metal Is Anodized?
Anodized metal often has a distinctive, durable finish that can be identified by color. Colors can vary depending on the alloy and the anodizing process used. Additionally, anodized surfaces feel harder and smoother compared to untreated metal. If you scratch the surface, the color will remain consistent as the color is integrated into the oxide layer.
How Long Does Anodized Last?
The longevity of anodized finishes depends on factors such as the type of alloy, the anodizing process used, and the environmental conditions. Anodized coatings are durable and can last for many years. With proper care and maintenance, they can maintain their appearance and functionality for a long time.
Does Anodizing Prevent Rust?
Yes, anodizing helps prevent rust on metals. The anodizing process creates a protective oxide layer on the surface of the metal, which acts as a barrier against corrosion. This makes anodized aluminum more resistant to rust and other forms of oxidation. However, it’s essential to note that anodized coatings can be compromised if they are scratched deeply or damaged.