Custom Shaft Machining & Manufacturing
We brings a wealth of experience from crafting thousands of custom shafts, ensuring your project benefits from high efficiency, precision, cost-effectiveness, and swift delivery.
- Over 40 Certified Materials
- Custom Finishes
- No Minimum Order
- Fast Turnaround
Save 30% on average!
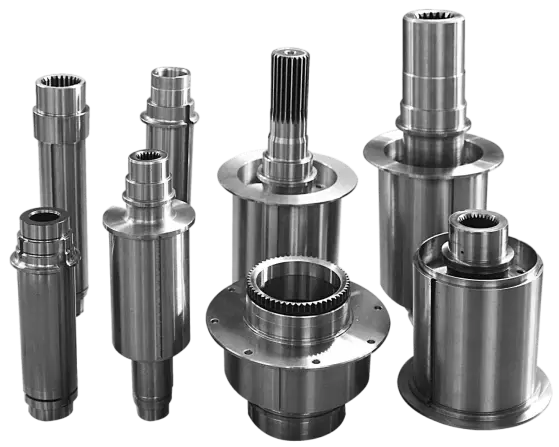
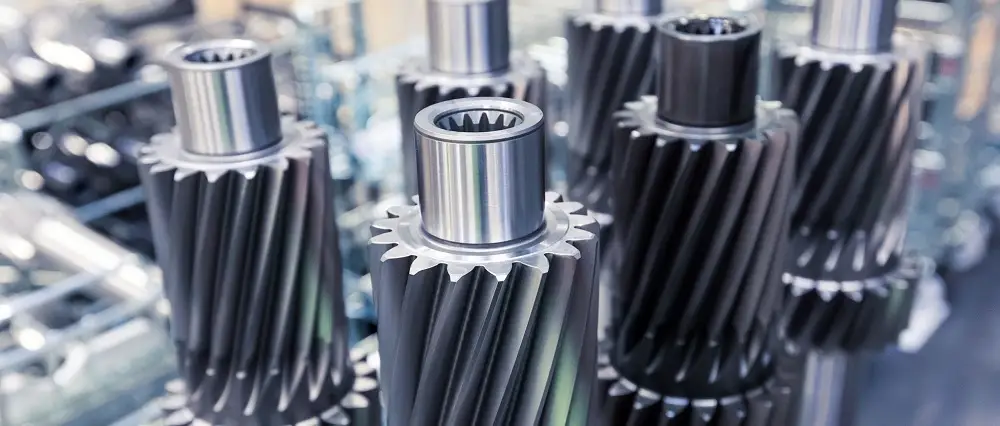
What Is Custom Shaft Manufacturing?
Custom shaft manufacturing is the process of creating specialized shafts designed to meet the unique requirements of a particular application or project. It involves a collaborative effort between the customer and the manufacturer to engineer the shaft, selecting the appropriate materials, dimensions, and surface treatments. Advanced manufacturing techniques, such as CNC machining and specialized fabrication processes, are then employed to produce the custom shaft to the desired level of precision and quality.
This flexibility allows engineers and designers to optimize their mechanical systems, improve efficiency, and overcome the limitations of off-the-shelf components. Custom shaft manufacturing is particularly valuable in industries like aerospace, automotive, and industrial machinery, where tailored solutions are often required.
our expertise in custom shaft manufacturing ensures unparalleled quality and precision. Discover our tailored process that seamlessly aligns with your product requirements, and elevate your production experience by partnering with us.
How To Machining Customized Shaft?
The key machining steps involved in producing customized shafts include advanced CNC (Computer Numerical Control) techniques such as turning, milling, and grinding. These precise fabrication methods are used to manufacture the shaft to the required dimensional accuracy, surface finish, and any specialized features like keyways or splines. Specialized processes like induction hardening may also be employed to enhance the shaft’s material properties and performance characteristics. Careful quality control measures are implemented throughout the machining process to ensure the final product meets the customer’s exact specifications.
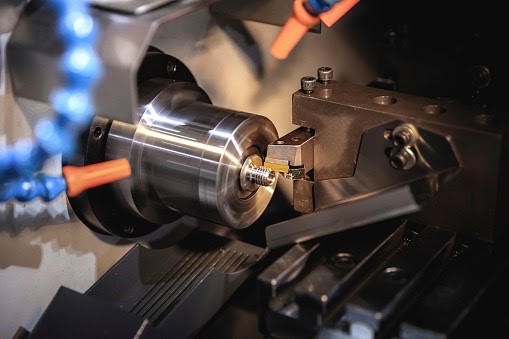
CNC turning is a crucial machining process for manufacturing custom shafts, enabling the precise fabrication of the shaft's cylindrical geometry and dimensions.
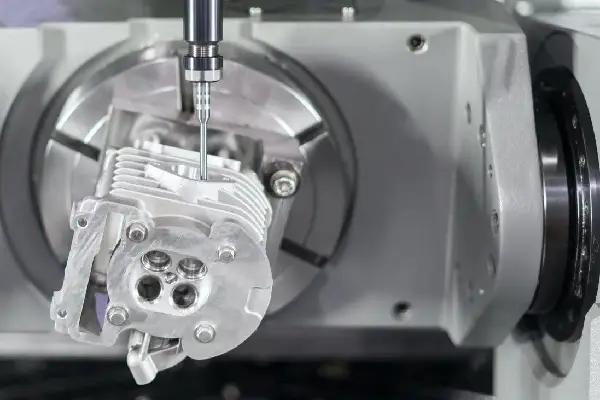
CNC milling is used to create specialized features on custom shafts, such as keyways, splines, and stepped diameters, improving functionality and component integration.
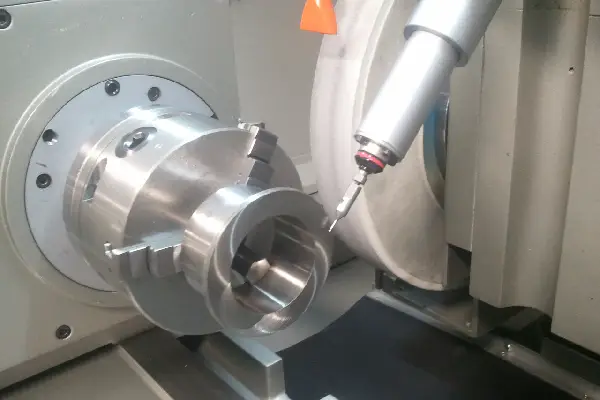
CNC grinding provides the final surface finish on custom shafts, ensuring tight dimensional tolerances and exceptional surface quality for optimal performance.
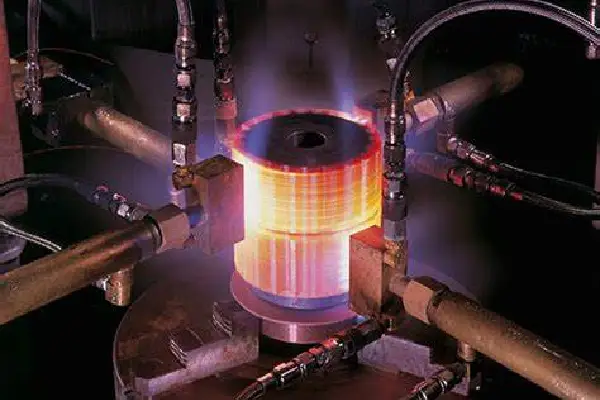
Heat treatment processes can be used to enhance the strength, hardness, and wear resistance of custom shaft materials, improving the shaft's overall durability.
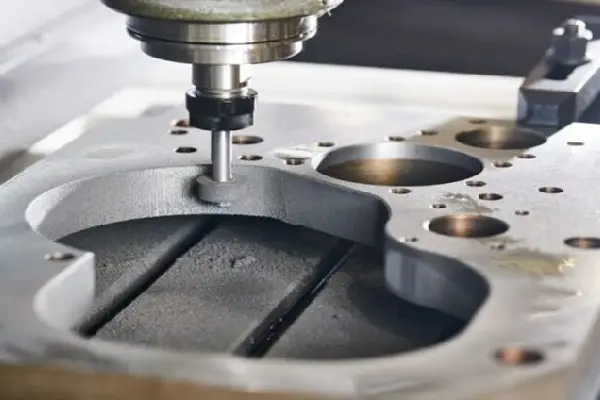
Surface finishing techniques, such as polishing or honing, are used to achieve the desired surface roughness and minimize friction on custom shafts.
Material Selection For Custom Shafts
Steel
Widely used for its strength, durability, and cost-effectiveness, available in various grades and alloys to meet specific performance requirements.
Stainless Steel
Offers excellent corrosion resistance, making it suitable for harsh environments, available in different grades like 304 and 316.
Aluminum Alloy
Lightweight yet strong, making it suitable for applications where weight reduction is important, easy to machine and finish.
Brass
A copper-zinc alloy with good corrosion resistance, machinability, and aesthetic appeal, often used in decorative or low-load applications.
Titanium Alloy
Extremely strong and lightweight, with excellent corrosion resistance, commonly used in aerospace and medical applications.
Composite Materials
Fiber-reinforced composites, such as carbon fiber or fiberglass, provide exceptional strength and low weight for specialized applications.
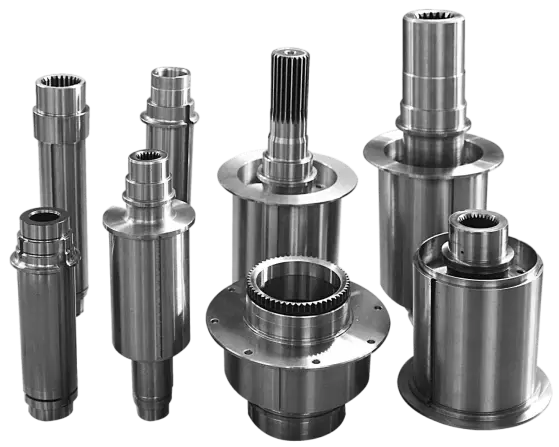
The Most Common Types Of Shafts
Solid Shaft: A single, continuous cylindrical piece of material, the simplest and most basic shaft type, commonly used in low-power and low-speed applications like hand tools and small machinery.
Hollow Shaft: Also known as a tubular shaft, it has a hollow, cylindrical design with a central bore, making it lighter in weight compared to solid shafts, suitable for weight-sensitive applications.
Stepped Shaft: Features two or more diameters along its length, allowing it to accommodate various components like bearings, gears, or pulleys, providing a way to transition between different component sizes.
Tapered Shaft: Has a gradually decreasing or increasing diameter along its length, enabling a secure fit for components like pulleys or gears that need to be mounted on the shaft.
Splined Shaft: Incorporates a series of parallel grooves or ridges, called splines, running along its length, allowing the shaft to transmit torque and power to connected components.
Keyed Shaft: Has a flat surface or groove, called a keyway, running along its length, providing a secure mounting point for components like pulleys or gears, preventing them from slipping.
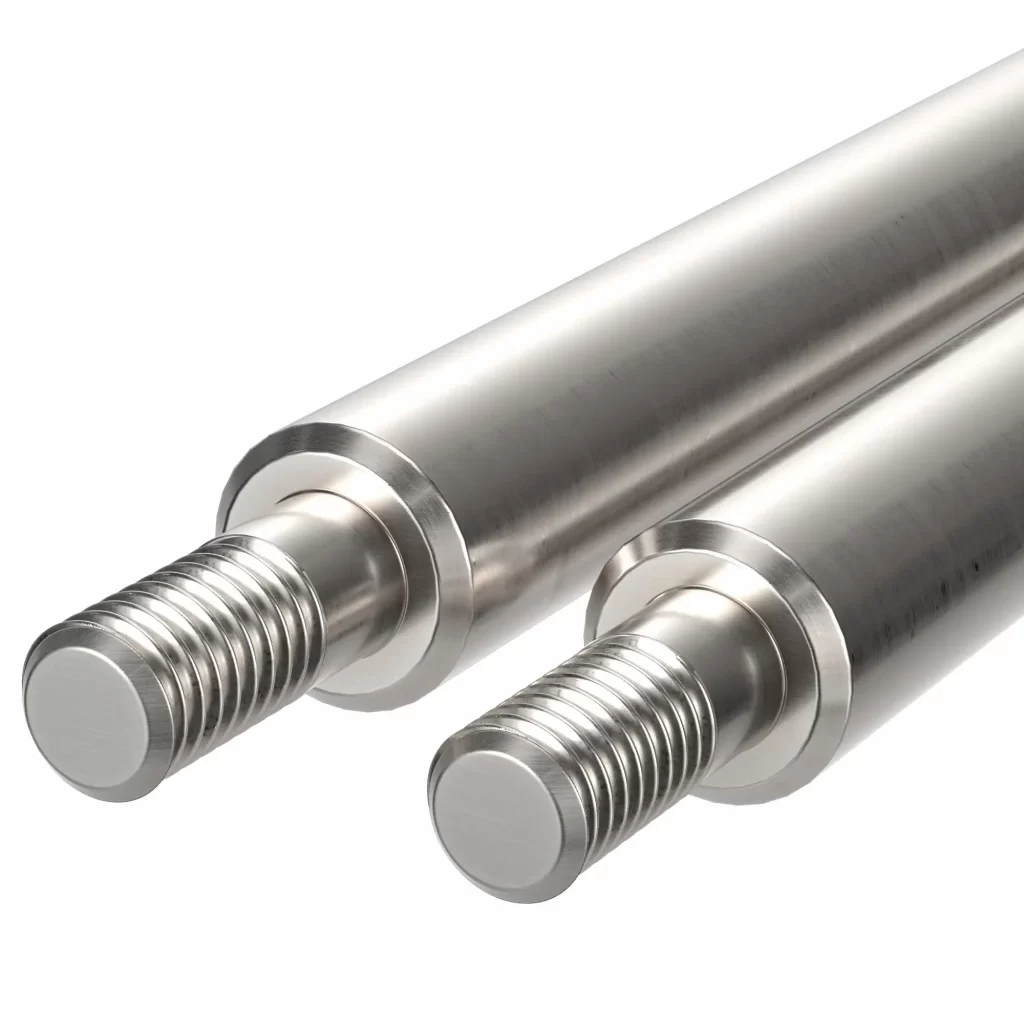
What is the machining process for shafts?
he machining process for custom shafts typically involves several key steps. First, the shaft design is engineered to meet the specific requirements. Advanced CNC (Computer Numerical Control) techniques, such as turning, milling, and grinding, are then employed to fabricate the shaft to precise dimensions and surface finishes. Rigorous quality control measures are implemented throughout the manufacturing process to ensure the final product meets or exceeds the customer’s expectations.
Which material Cannot be used to manufacture shafts?
Certain materials are generally not suitable for manufacturing shafts due to their inherent properties. For example, materials with low strength, poor fatigue resistance, or high susceptibility to corrosion would not be appropriate choices for shaft applications that require reliable and durable performance.
What are the Challenges of Machining Customized Shafts?
Dimensional Accuracy: Maintaining tight tolerances on critical dimensions to ensure proper fit and function of mounted components, requiring precision CNC machining and robust quality control measures.
Complex Geometries: Integrating specialized features like splines or tapered sections while maintaining accuracy and surface quality, necessitating sophisticated machining techniques and skilled programming capabilities.
Material Variations: Adapting machining processes to accommodate the unique properties of different shaft materials, such as hardness or toughness, to ensure consistent quality and productivity.
What industries commonly utilize custom shaft manufacturing?
Custom shaft manufacturing is widely used in industries like aerospace, industrial machinery, automotive, and specialized equipment, where tailored solutions are often required to meet unique application needs.