Precision CNC Milling Services in China
China high-quality precision CNC milling services you can trust. Competitive pricing and fast lead times.
- Over 60 Certified Materials
- ±0.005mm Tight Tolerance
- Custom Finishes
- Lead times from 7 days
- Customer data security
Save 30% on average!
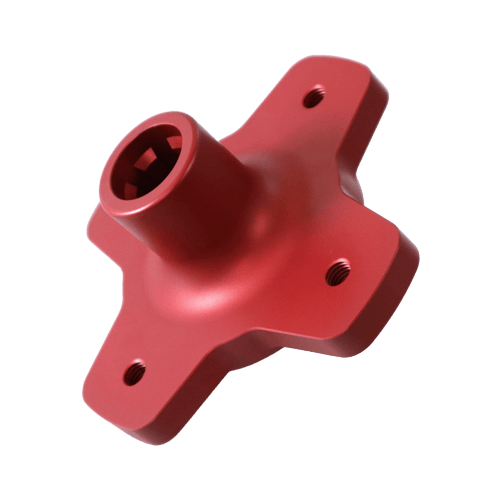
Vertex is the premier supplier of CNC-milled parts. Our experienced engineers, designers, and procurement units ensure that our services are provided efficiently and cost-effectively for all project needs ranging from prototypes to mass production runs.
All this, backed by high-tech milling centers with a wide range of finishing options, allows us to deliver top-notch quality quickly, reliably, and flexibly – perfect for your precision manufacturing requirements!
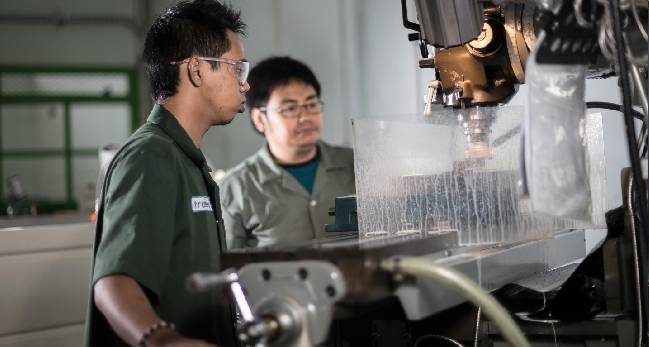
Experience unparalleled accuracy and quality in your prototyping and production runs with our cutting-edge 3 and 5-axis milling centers. Attain the highest performance standards while crafting intricate parts that fulfill even the most stringent requirements.
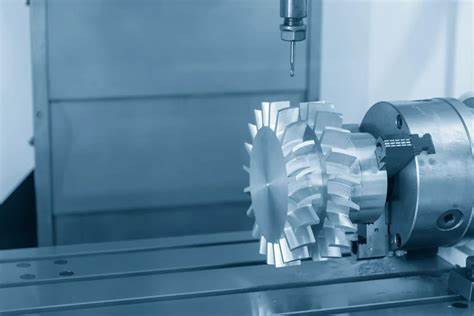
3-axis and 3+2 axis CNC milling machines provide an economical solution for producing parts with simpler geometries. These systems offer a low cost of entry as compared to other machining processes, making them ideal choices where affordability is critical.
Size
Metric units
Imperial units
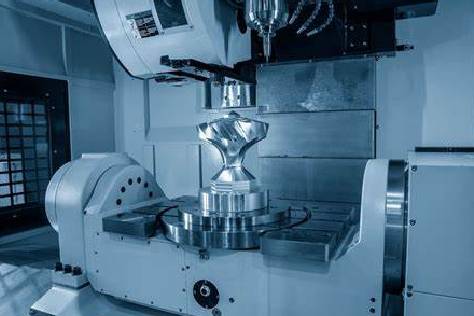
5-axis CNC milling centers have the capability to deliver superior quality parts while markedly increasing efficiency. With fewer setups required, they offer a cost-effective solution for achieving complex geometries quickly and accurately.
Size
Metric units
Imperial units
Vertex provides a variety of CNC machining tolerances tailored to your specific design needs, including GD&T callouts. Depending on your part’s geometry and selected material, we accommodate standard and custom thread sizes, achieving tolerances up to ±0.001″. Our default CNC milling tolerances for metals follow ISO 2768-m, while for plastics, we adhere to ISO 2768-c.
Type
Tolerance
Vertex offers a wide variety of materials for custom CNC machining, plastic, and metal, including but not limited to:
Aluminum: Aluminum’s strength-to-weight ratio, affordability, and recyclability have made it widely used across industries worldwide.
Alloys: 6061-T6, 7075-T6, 2024, 5052, 6060, 5083, 2017, 6082
Finishing Options: Alodine, Anodizing Types II, III, III + PTFE, ENP, Media Blasting, Nickel Plating, Powder Coating, Tumble Polishing
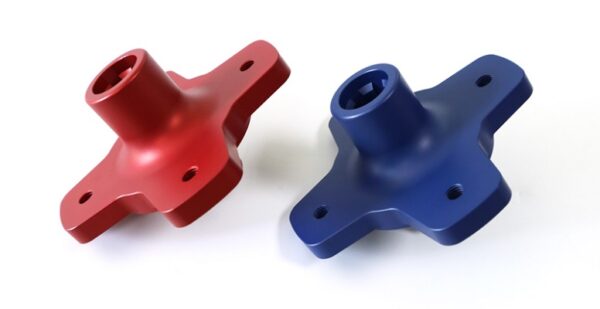
Stainless steel: Stainless steel’s corrosion resistance and ductility make it ideal for long-term exposure to elements and easy shaping into different forms
Finishing Options: As machined, Bead Blasted, Polishing, Decorative Chrome Plating, Powder Coat, Nickel Plating, Gold Plating, Silver Plating
Alloys: SS303, Stainless Steel 304/304L, Stainless Steel 316/316L, Stainless Steel 17-4, Stainless Steel 416, etc.
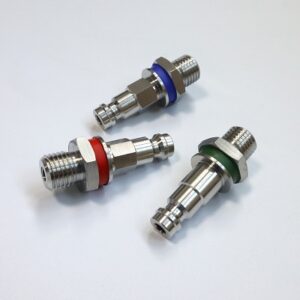
Alloy Steel: Alloy steel is steel mixed with elements like manganese, nickel, and chromium to enhance its strength, hardness, corrosion resistance, and durability, tailored to meet specific application needs.
Alloy: AISI 1215, AISI 4140, AISI 4340, AISI 8620, AISI 4130
Finishing Option: Polishing, Plating, Painting, Powder Coating and etc.
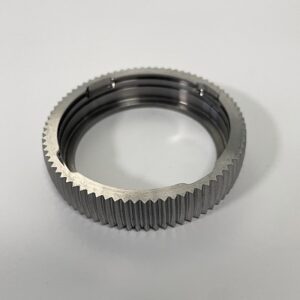
Tool Steel: Tool steel is a type of high-carbon and high-alloy steel that is specifically designed to be used in the manufacture of cutting tools, dies, and molds. It is valued for its high hardness, wear resistance, and toughness, which make it suitable for applications where the tool is subjected to repeated impacts or stresses.
Alloy: A2 Tool Steel, D2 Tool Steel, O1 Tool Steel, S7 Tool Steel, M2 Tool Steel
Finishing Option: Bead/Sand Blast, Polishing, Plating, Painting, Powder Coating, Heat Treatment and etc.
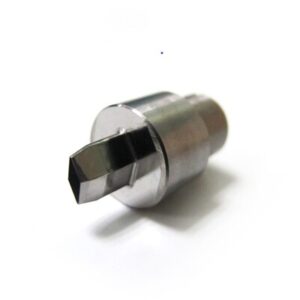
Brass: Brass is an alloy of copper and zinc, especially metal material with more than 20% zinc content, which is the most commonly used metal material in cnc machining
Finishing Options: Nickel Plating, Bead Blasted, Gold Plating, Silver Plating
Alloy: C360, C260
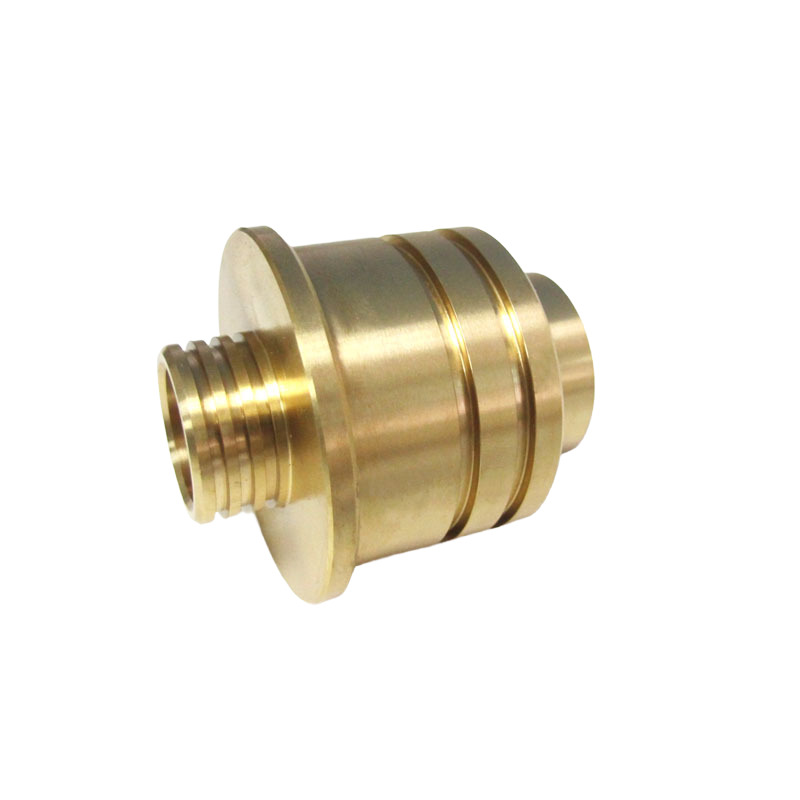
Copper: Copper is a soft, malleable metal with excellent thermal and electrical conductivity, making it an essential material in many industries.
Grade: C10100, C11000, C12200, C14500, C17200
Finishing Option: Plating, Polishing
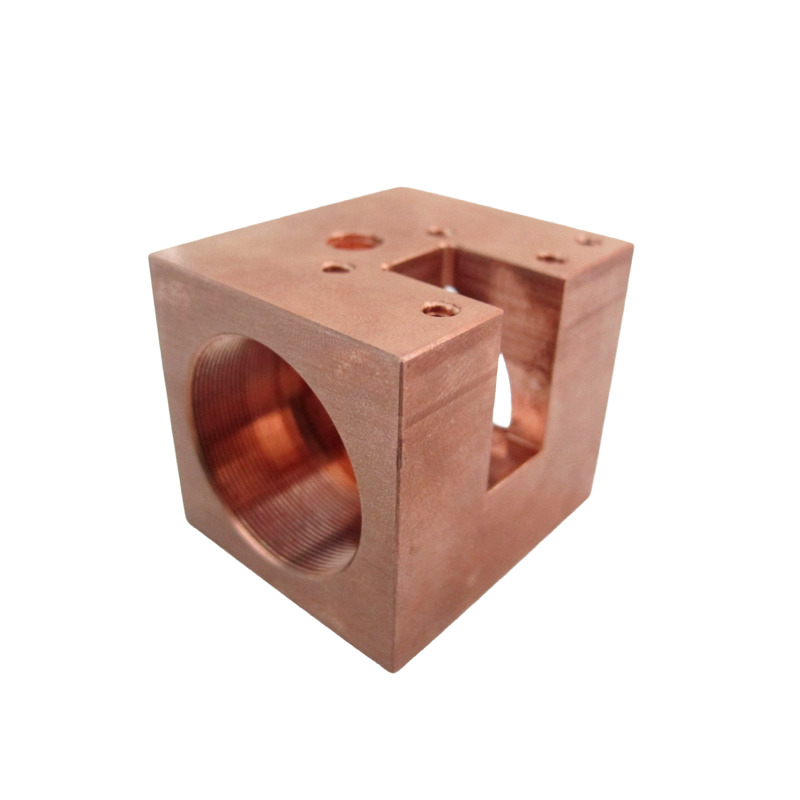
Titanium:Titanium has a low density and high strength, making it ideal for applications that require a strong yet lightweight material, such as aerospace, automotive, and biomedical industries. It is also highly resistant to corrosion and can withstand exposure to many chemicals and environments
Alloy: Ti-6Al-4V, Ti-6Al-2Sn-4Zr-2Mo, Ti-3Al-2.5V
Finishing Option: Polishing, Anodizing, Sandblasting, Chemical etching, Laser engraving and etc.
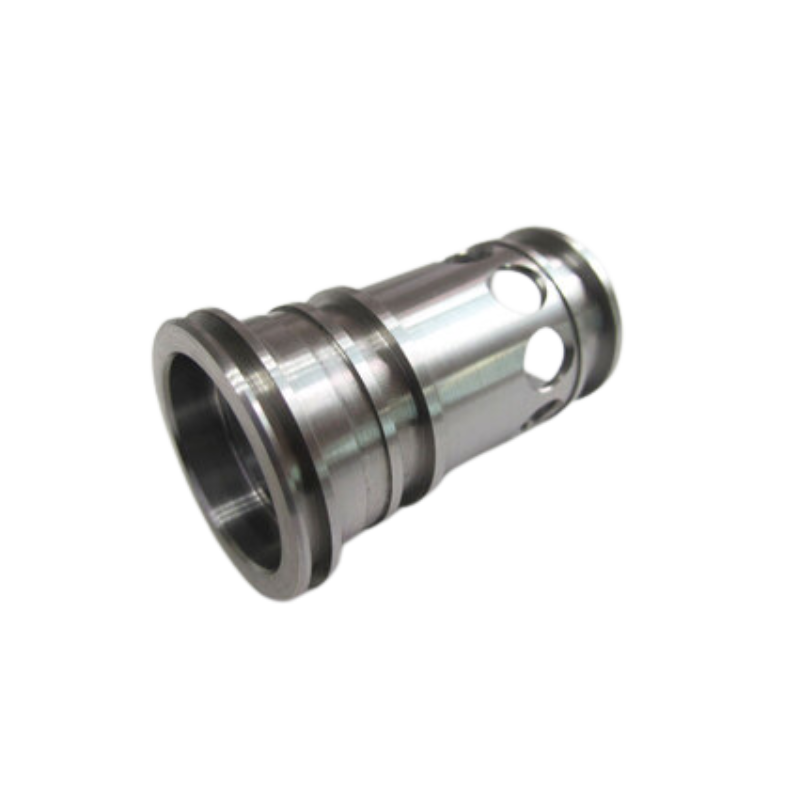
POM (Delrin/Acetal): High stiffness, good moisture resistance, high wear-resistance, and low friction, easy to machine
Color: White, black, brown
Grade: POM-C, POM-H, UV stabilized POM, Food-Grade POM
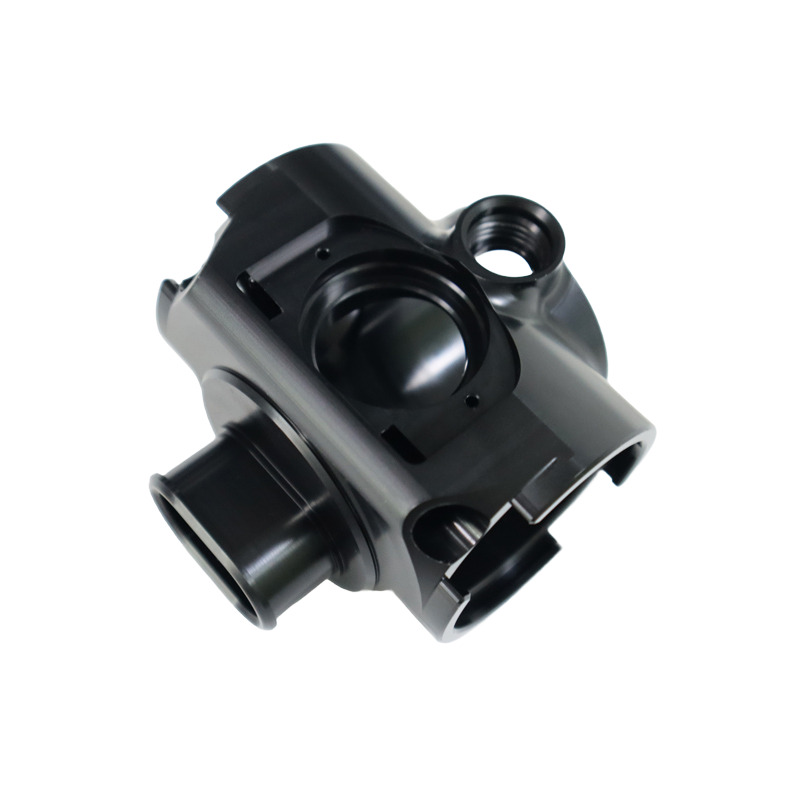
PMMA: PMMA is commonly known by the trade name “acrylic” or “plexiglass”. It is a lightweight and shatter-resistant material that is often used as a glass substitute in applications such as skylights, displays, signage, and lenses
Color: Transparency
Grade: Extruded PMMA, Cast PMMA, Impact-Modified PMMA, UV-Stabilized PMMA, Heat-Resistant PMMA
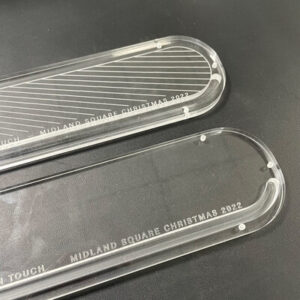
PEEK: PEEK is a high-performance engineering thermoplastic with excellent mechanical, chemical, and thermal properties, short for Polyether Ether Ketone
Color: Beige with no transparency
Grade: Unfilled PEEK, 30% glass-fiber reinforced PEEK, 30% carbon-fiber-reinforced PEEK, Bearing Grade PEEK
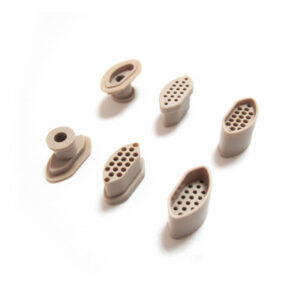
ABS: ABS is tough, rigid, and lightweight, making it an excellent material for use in applications such as automotive parts, toys, electronic housings, and consumer goods. It is also resistant to impact, chemicals, and heat, making it a popular choice for use in harsh environments
Color: ABS is naturally opaque and comes in a range of colors including black, white, and gray
Grade: General purpose ABS, Flame retardant ABS, High impact ABS, Heat-resistant ABS
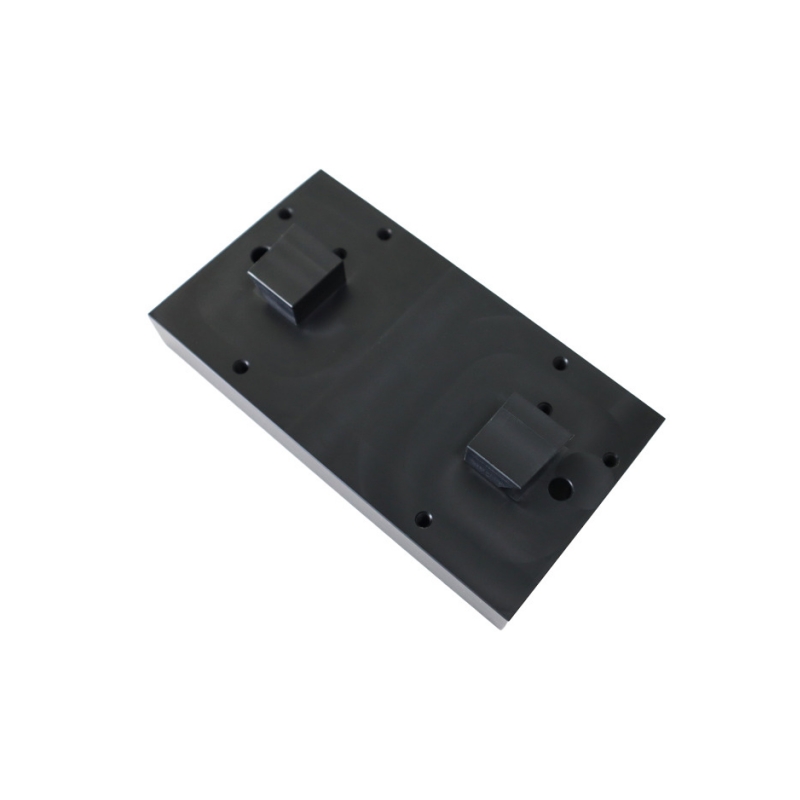
Nylon: Nylon is a strong, durable, and elastic material that is commonly used in textiles like clothing and ropes. Its resistance to abrasion, chemicals, and moisture makes it popular for industrial applications, such as gears, bearings, and automotive components
Color: Nylon is often used in its natural off-white or slightly yellowish color
Grade: Nylon 6, Nylon 6/6, Nylon 11, Nylon 12
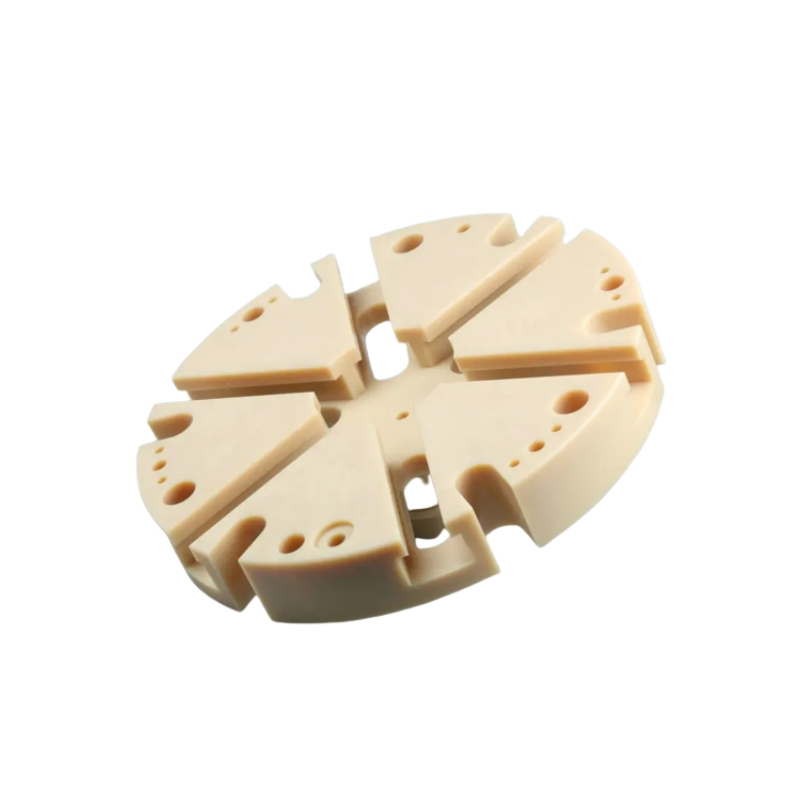
PTFE: PTFE(Teflon) is a high-performance plastic material known for its exceptional chemical resistance, low friction coefficient, and high-temperature resistance
Color: The color of PTFE is typically white or off-white
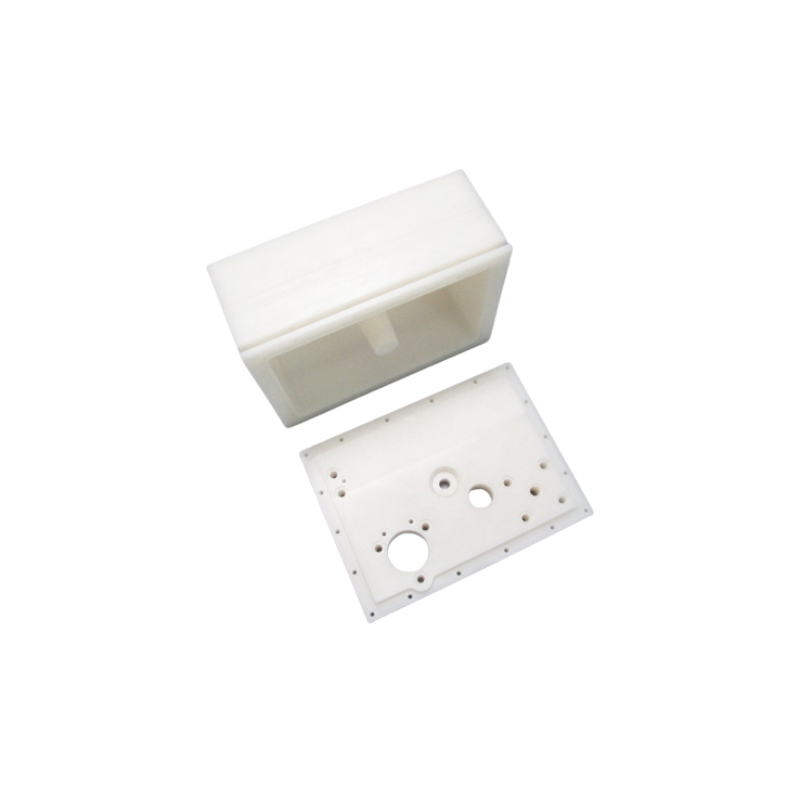
PVC: PVC stands for polyvinyl chloride, which is a synthetic thermoplastic polymer that is widely used in various applications. PVC is a versatile material that can be rigid or flexible
Color: clear or opaque
Grade: UPVC, PPVC, CPVC
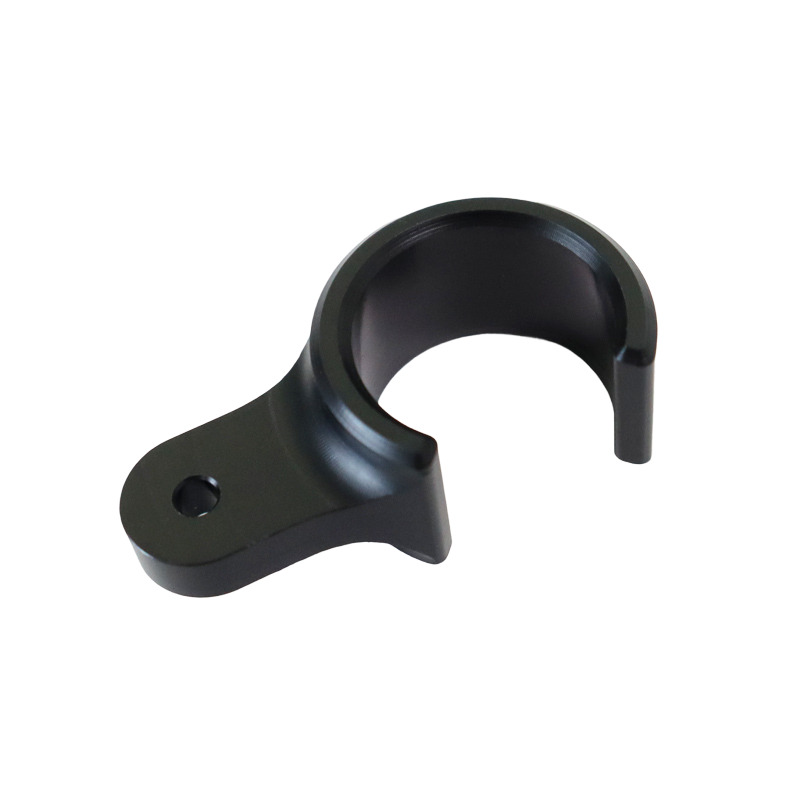
PEI: PEI has excellent mechanical, thermal, and electrical properties, as well as good chemical resistance
Color: Amber or brownish color
Grade: Unfilled PEI, Glass-Filled PEI, Carbon-Filled PEI, Ultem PEI
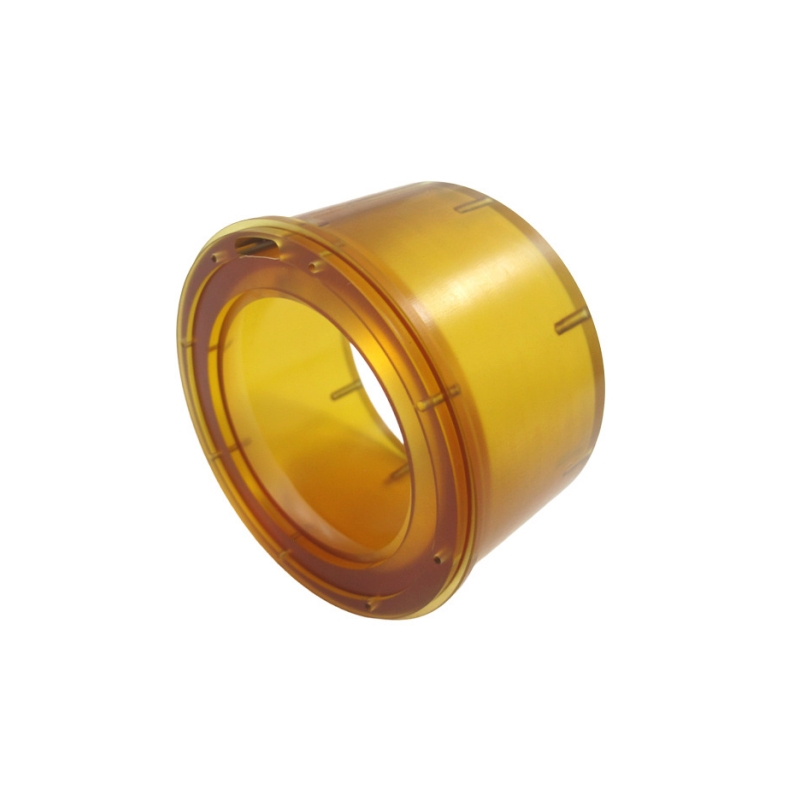
Surface Finishes For CNC Machined Parts
Apart from custom CNC machining services, we also provide complete surface finishing options for precision machined parts. If you require custom finish not on this list, please do get in touch as it is likely we can source it for you.
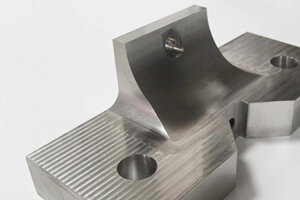
This finishing option with the shortest turnaround time. Parts have visible tool marks and potentially sharp edges and burrs, which can be removed upon request.
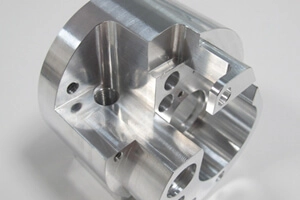
Smooth machining is similar to a ‘As machined’ finish, but with less visible machine marks. Parts are machined at a lower feed rate, with no hand polishing.
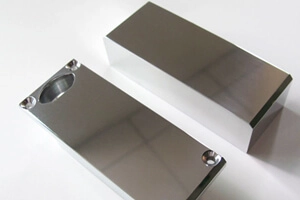
Polishing is the process of creating a smooth and shiny surface by rubbing it or by applying a chemical treatment.
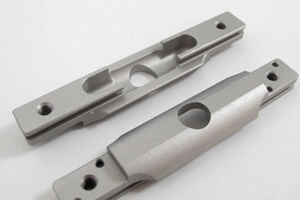
Machined parts are bead blasted with glass beads which results in a uniform grainy texture and reduced machining marks.
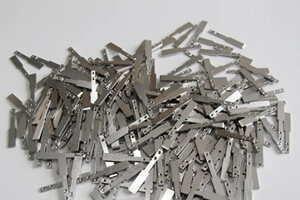
It is a process that tumbles vibrating media on machined parts to remove sharp edges and burrs.
Tumbling can be used to remove machine marks from exterior surfaces.
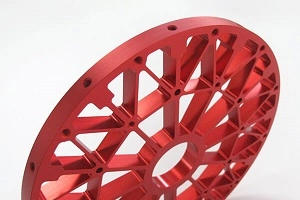
The parts are bead blasted to #120 grit before being anodized type II—ideal for increasing the aluminum part’s corrosion resistance and cosmetic effects.
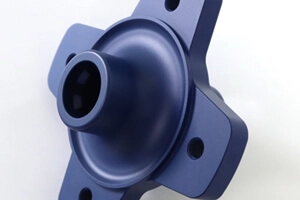
The parts are bead blasted to #120 grit before being anodized type III. Type III (Hard Coat) is thicker and adds a wear-resistant layer to Type II’s corrosion resistance, suitable for functional applications.
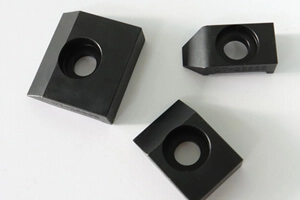
Black oxide is a conversion coating that is used on steels to improve corrosion resistance and minimize light reflection.
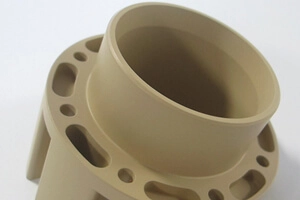
This is a finish of applying powdered paint to the components and then baking it in an oven, which results in a stronger, more wear- and corrosion-resistant layer that is more durable than traditional painting methods.
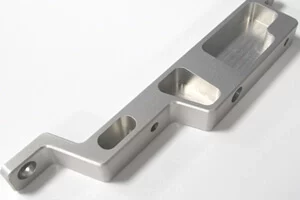
Chromate conversion coating is used to improve the corrosion resistance of aluminum and aluminum alloys while keeping their conductive properties. It is also applied as a base layer prior to priming and painting parts.
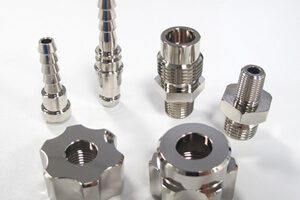
Include Nickel Plating, Silver Plating, Gold Plating, Zinc Plating, Chrome Plating, Tin Plating and etc, it is ideal to reduce corrosion, improve the appearance and function of solderability and electrical conductivity.
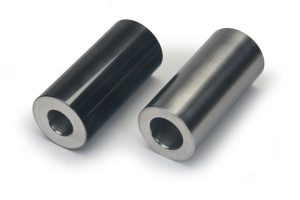
DLC (Diamond-Like Carbon) coating is a hard, wear-resistant coating made of a carbon-rich material that exhibits some of the properties of diamonds.
By incorporating state-of-the-art milling machines, streamlining our production processes, and buying our raw materials in bulk quantities, we're able to minimize your expenses by anywhere from 30% to 60%.
Our standard CNC tolerance is +/- 0.127mm, and when you use our tolerance configurator, you can expect precision machining to +/- 0.005mm.
Our team guarantees exceptional after-sales service and solutions and takes full responsibility in resolving any potential issues. We never turn a blind eye, but proactively tackle challenges head-on to ensure our customers are satisfied.
We offer high-quality finishing processes for most CNC Milled parts, including anodizing, polishing and plating, heat treatment, powder coating, DLC coating, and more.
We offer over 60 production grade materials, and take great care to ensure the right material is used for every part.
Send in your CNC Milled parts order today and experience a painless, streamlined process that will get you quality results with a fast turnaround - guaranteed to reach as quickly as 7 days!
We machine rapid prototypes and low & large volume production orders for customers in multiple industries: medical devices, aerospace, automotive, defense, electronics, hardware startups, industrial automation, machinery, marine and robotics, and many more.
CNC Milling FAQs
What is tool offset in CNC milling?
Tool offset in CNC milling is like adjusting a pencil or a pen in your hand while drawing or writing. Imagine each tool as a different pencil with various lengths and widths. When you switch between them, you need to make slight adjustments to ensure your drawing or writing remains accurate and consistent.
Similarly, in CNC milling, tool offset is a way to fine-tune different cutting tools’ positions to ensure they follow the right path and depth while machining a part. By adjusting for the differences in tool sizes and wear, the milling machine can create accurate and precise parts, even when using multiple tools with different dimensions.
What is 5-axis CNC machining?
5-axis CNC machining is a method used to create complex parts using a computer-controlled machine. Imagine it as an advanced robotic sculptor that can move its carving tool in five different directions to shape a piece of material.
In simpler terms, the machine’s cutting tool can move along three basic directions—up and down, left and right, and forward and backward. These movements are referred to as the X, Y, and Z axes. In addition to these three, the tool can also rotate around two of these axes, allowing it to reach more angles and sides of the material. This is where the “5-axis” term comes from, as it represents the three linear movements plus the two rotational movements.
Because of these extra movements, 5-axis CNC machines can create intricate shapes and designs that would be challenging or impossible to achieve with traditional 3-axis machines, which can only move in the X, Y, and Z directions without rotation. This advanced capability allows for faster production, better accuracy, and more complex parts.
What is the difference between CNC turning and CNC milling?
In CNC turning, the material (usually a metal or plastic rod) is held and rotated at high speed, while a cutting tool moves to remove the unwanted material, shaping the part. It’s similar to how a potter shapes clay on a spinning wheel. This process is best for creating cylindrical or round parts.
On the other hand, CNC milling is like the sculptor using a chisel to shape a block of material. The material stays stationary while the cutting tool moves around and across it, cutting and carving the material into the desired shape. CNC milling can create more complex shapes and is suitable for both flat and curved surfaces.
What is the difference between a CNC router and a CNC mill?
A CNC router is designed to cut materials like wood, plastic, foam, and sometimes soft metals like aluminum. It has a large working area and usually moves at higher speeds. The router’s cutting tool, called a spindle, is designed for cutting flat surfaces and intricate patterns, similar to a high-speed carving machine. CNC routers are typically used for woodworking, sign-making, and other applications that require speed and precision on large, flat materials.
The CNC mill is more robust and versatile, capable of handling harder materials like steel, brass, and titanium. It is built to withstand the force and precision required for cutting these materials. The cutting tools in a CNC mill, called end mills, can move in multiple directions, enabling the machine to create more complex shapes and designs.
What types of materials do CNC mills use?
Metals: CNC mills can work with a range of metals, from softer ones like aluminum and brass to harder ones like steel, stainless steel, and titanium. These machines are often used in industries like automotive, aerospace, and metalworking to create precise metal parts.
Plastics: CNC mills can also shape various plastic materials, including acrylic, PVC, polyethylene, and nylon, among others. These plastics are often used in the manufacturing of medical devices, consumer products, and electronic components.
Composites: CNC mills can handle composite materials made from a combination of different substances, like carbon fiber, fiberglass, and Kevlar. These composites are often used in the aerospace, automotive, and sporting goods industries.
Ceramic: CNC milling machines can precisely shape and cut various types of ceramics, including alumina, zirconia, silicon carbide, and silicon nitride. Due to the brittle nature of ceramics, the milling process requires special attention to factors like cutting speed, tool selection, and cooling to prevent cracking or chipping of the material.