Carburizing Heat Treatment for Your Custom CNC Parts
Carburizing heat treatment infuses carbon into steel or iron surfaces at high temperatures, enhancing hardness and wear resistance while maintaining a tough, ductile core.
- Over 40 Certified Materials
- Custom Finishes
- No Minimum Order
- Fast Turnaround
Save 30% on average!
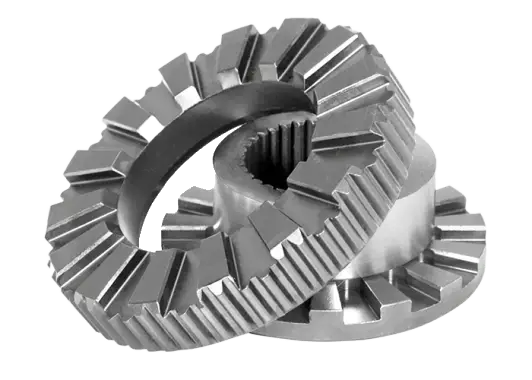
How Steel And Iron Carburizing Works
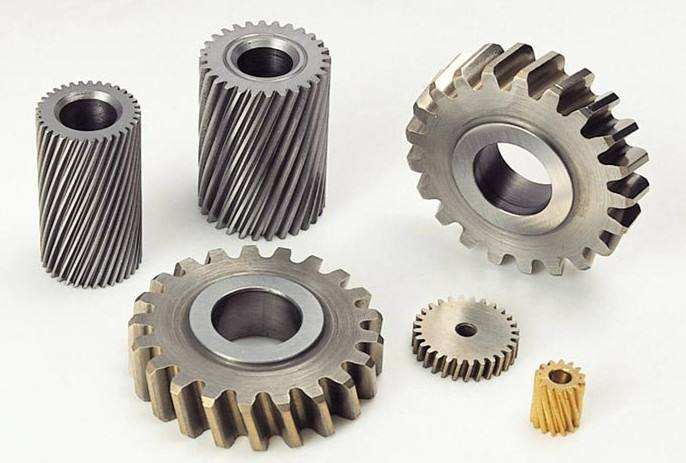
Carburizing is a heat treatment process used to enhance the surface hardness of steel and iron components. The process begins by heating the metal to a high temperature, typically between 850°C and 950°C, in a carbon-rich environment.
This environment can be created using gas, liquid, or solid carbon sources. As the metal is heated, carbon atoms diffuse into the surface, increasing its carbon content.
After sufficient carbon penetration, the component is rapidly cooled or quenched, locking the carbon in place and creating a hard, wear-resistant outer layer while maintaining a tough, ductile core.
This dual-phase structure improves durability and performance.
Important Details To Get Perfect Carburized Parts
The six most important details to pay attention to during the carburizing process, which can significantly impact the final result.
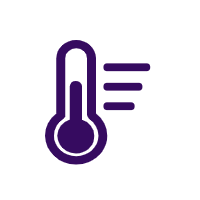
Maintaining precise temperatures (typically 850°C to 950°C) is crucial for effective carbon diffusion and achieving the desired case depth and hardness.
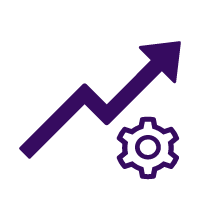
Regulating the carbon content in the carburizing atmosphere ensures consistent carbon uptake by the metal surface, affecting the final hardness and wear resistance.
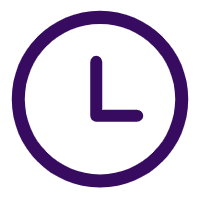
The duration of exposure to the carburizing environment determines the depth of carbon penetration. Longer times increase case depth but must be balanced to avoid excessive grain growth.
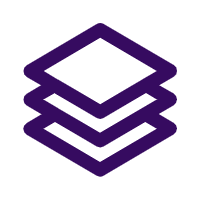
The base material's composition affects its response to carburizing. Alloying elements like chromium, molybdenum, and nickel can influence hardenability and case depth.
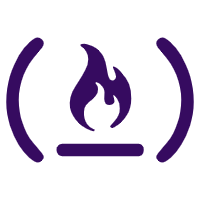
The cooling rate after carburizing impacts the hardness and microstructure of the case. Proper quenching media (oil, water, or air) should be selected based on the desired properties.
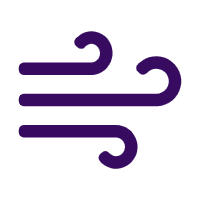
Maintaining a controlled atmosphere prevents oxidation and decarburization, ensuring the surface quality and integrity of the carburized layer.
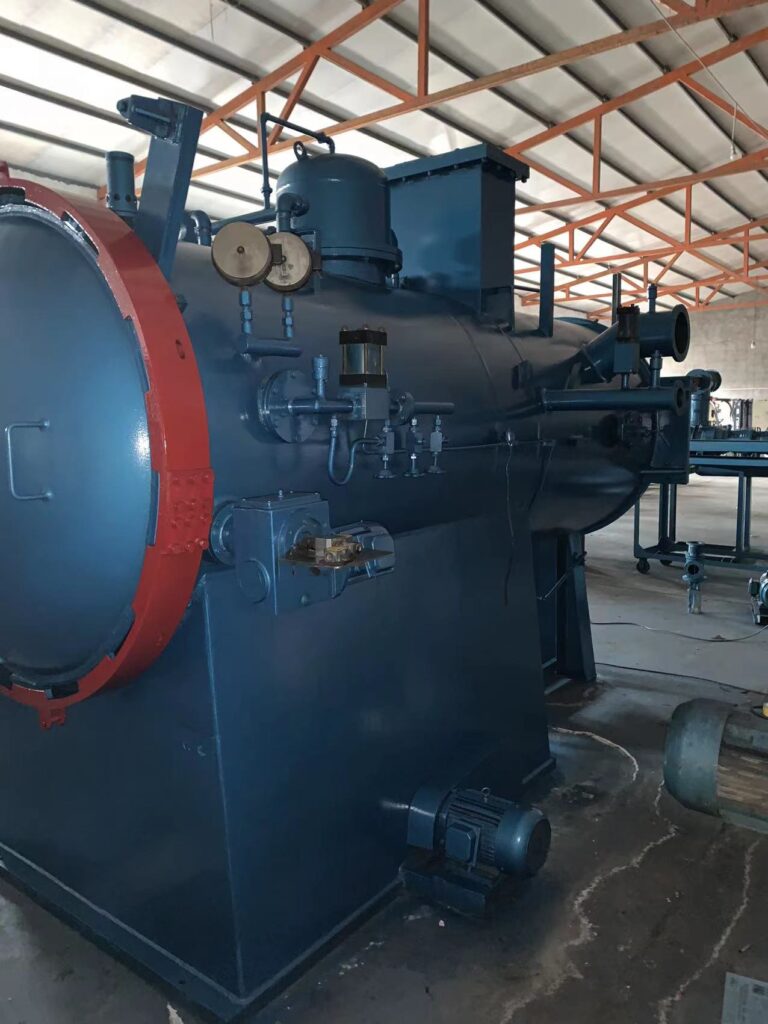
- Pack Carburizing: Involves placing the component in a sealed container with carbon-rich materials (charcoal or carbon powder) and heating it. Carbon diffuses into the metal surface, creating a hard outer layer.
- Gas Carburizing: Uses a carbon-rich gas (like methane or propane) in a furnace. The gas decomposes at high temperatures, allowing carbon to diffuse into the metal surface, forming a hardened case.
- Liquid Carburizing: Involves immersing the component in a molten salt bath containing carbonates and cyanides. High temperatures facilitate carbon diffusion into the metal surface, enhancing hardness.
- Vacuum Carburizing: Conducted in a vacuum furnace with controlled carbon gas introduction. This method ensures precise case depth and uniformity, reducing oxidation and contamination risks.
- Plasma Carburizing: Uses ionized carbon gases in a plasma field to enhance carbon diffusion into the metal surface. This method offers better control over case depth and reduced environmental impact.
- Low-Pressure Carburizing (LPC): Utilizes low-pressure carbon gases in a vacuum furnace. This technique provides precise control over carbon potential and case depth, minimizing distortion and enhancing component performance.